ARTICLE
MSD event data: a misleading indicator for workplace prevention
FOREWORD
This approach, although useful, has its limitations.
By focusing solely on these past events, many organizations risk obscuring crucial issues that do not appear in the statistics but which nevertheless cause long-term damage.
Why do organizations use data from recorded MSD events?
The common goal of organizations is to avoid musculoskeletal disorders (MSDs), which are serious for workers and costly for the organization. An MSD means a prolonged work stoppage, expensive medical care, and in some cases, functional limitations. For the company, this translates into a loss of productivity, an increase in direct and indirect costs, and a negative impact on employee morale.
Before the ergonomic issues at a workstation or department become more pronounced, the first “ergonomic” indicators surface like the first symptoms of an illness. At that point, if the causes are not identified and corrected, musculoskeletal disorders (MSDs) can develop into MSD events.
Instinctively, most organizations therefore rely mainly on data from recorded events to guide their future preventive actions and target the positions on which to intervene. Although this information is useful, it only tells part of the story.
Here are two reasons why it is necessary to go beyond these figures to truly prevent MSDs in your organization instead of just reacting to them:
The “healthy worker survivor effect”: an unknown bias
Have you ever noticed that certain difficult positions always seem to be occupied by the same type of workers? This phenomenon, known as the “healthy worker survivor effect”, can distort our perception of the real risks affecting certain positions. Generally, the employees who persist in the job are those who can best tolerate its difficult conditions, while their more vulnerable colleagues have left or simply changed (…).
The result?
Statistics on events involving MSDs for these jobs may appear artificially low, masking the presence of real risks.
Finally, a high turnover rate or difficulty in attracting new employees to a department or a specific job are warning signs, not shown in the MSD statistics, that managers should not ignore.
Cumulative effort: the silent enemy
Imagine a worker who does not handle any significant loads, but who, day after day, is subjected to repeated movements or restrictive postures without ever complaining or taking time off.
On paper, no MSD event is recorded.
However, the cumulative load over days, weeks and years gradually weakens the body. This slow and insidious wear and tear does not appear in the event statistics, but it represents a real risk to the long-term health of workers and the productivity of the company. It is a cumulative injury.
Managers must remain vigilant in the face of a frequent inability to meet production targets, as this can be a sign of fatigue resulting from excessive exposure to various risk factors.
Beyond the numbers: a comprehensive and proactive approach
Adopting a broader vision and a proactive attitude is essential to prevent issues affecting workers at source.
Here are a few points on the recommended intervention approach to anticipate issues instead of reacting to them:
- Listen to your workers: Their perceptions and feelings are valuable in detecting problems before they become statistics.
- Establish a diagnosis: This makes it possible to precisely target the problems to be solved and establish priorities for action beyond the recorded events.
- Assessing constraints, especially those that are often underrepresented in event data: Analyze workstations to identify and document risk factors (biomechanical/organizational/environmental), even in the absence of complaints.
- Taking action: Expertise is then translated into concrete and feasible solutions, in collaboration with workers and the various levels of the organization.
- Reassess, train and raise awareness: A culture of prevention requires all company stakeholders to understand the risks and preventive actions to be monitored to optimize prevention investments.
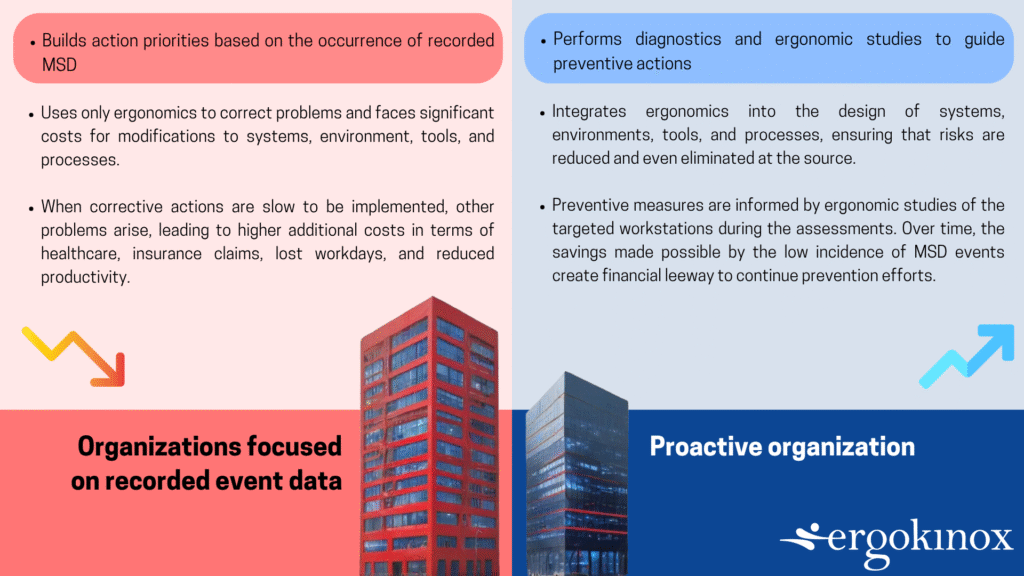
In short, although MSD event data is important, it should not be your only guide.